1. Introduction
Whilst circular textiles are the talk of the town amongst public and private value chain actors, conversations rarely unite actors of both worlds. Whilst the fashion industry strives to close their supply chains into a circular one, governments are facing a growing mountain of valueless discarded textiles. EigenDraads was established to create awareness amongst local governments, often responsible for waste management, on the recycling solutions for textiles that are emerging. Ambercycle is one of the frontrunning initiatives developing a solution to the textile waste problem. In 2019, Ambercycle and EigenDraads partnered to show the potential for chemical recycling to tackle the growing mountain of textile waste cities are facing across the globe. To do so, a garment was created from textile waste collected during the marathon of Rotterdam supplemented with other discarded Rotterdam textiles.
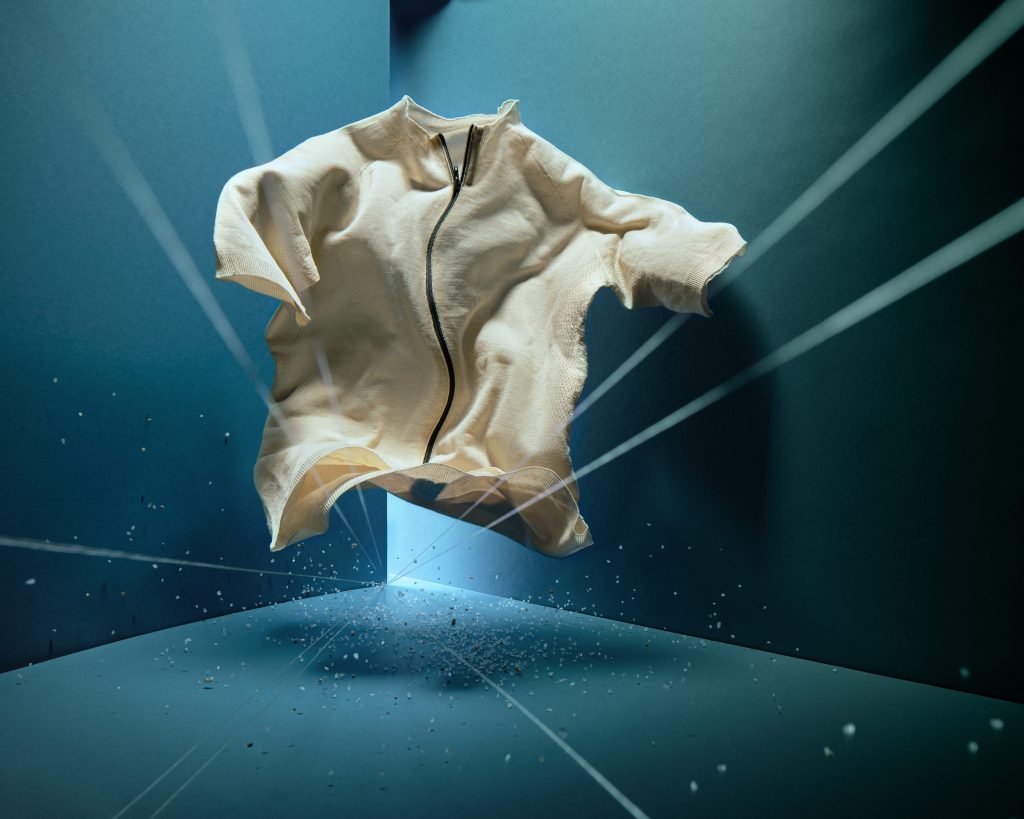
2. The garment and its process
Textiles left behind at the start of the Rotterdam Marathon were collected. A small share of resellable items was offered to local secondhand shops for resale. The non-resellable share was donated to EigenDraads for the pilot. Following the discarded marathon textiles were supplemented with other discarded Rotterdam textiles.
As a first step, hardware (like buttons and zippers) was removed by people with a distance to the labour market in Rotterdam’s sheltered workshop to assess the suitability of such activities for its employees. The work was well received, as some of the employees found the removal of hardware from textiles a less repetitive activity than their normal work on the packaging line.
In June 2019, the garments were shipped from Rotterdam to Los Angeles.
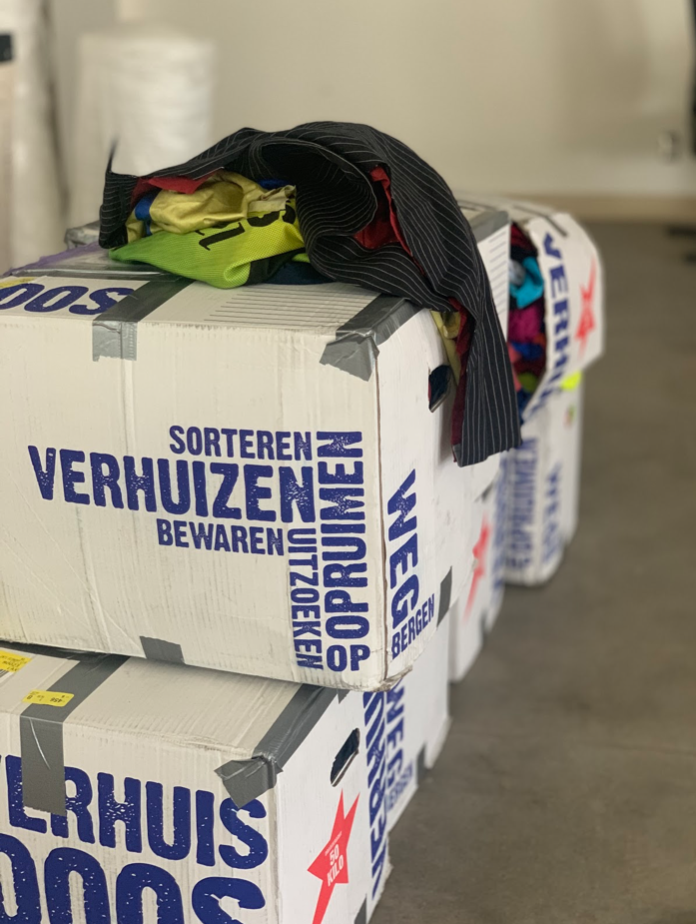
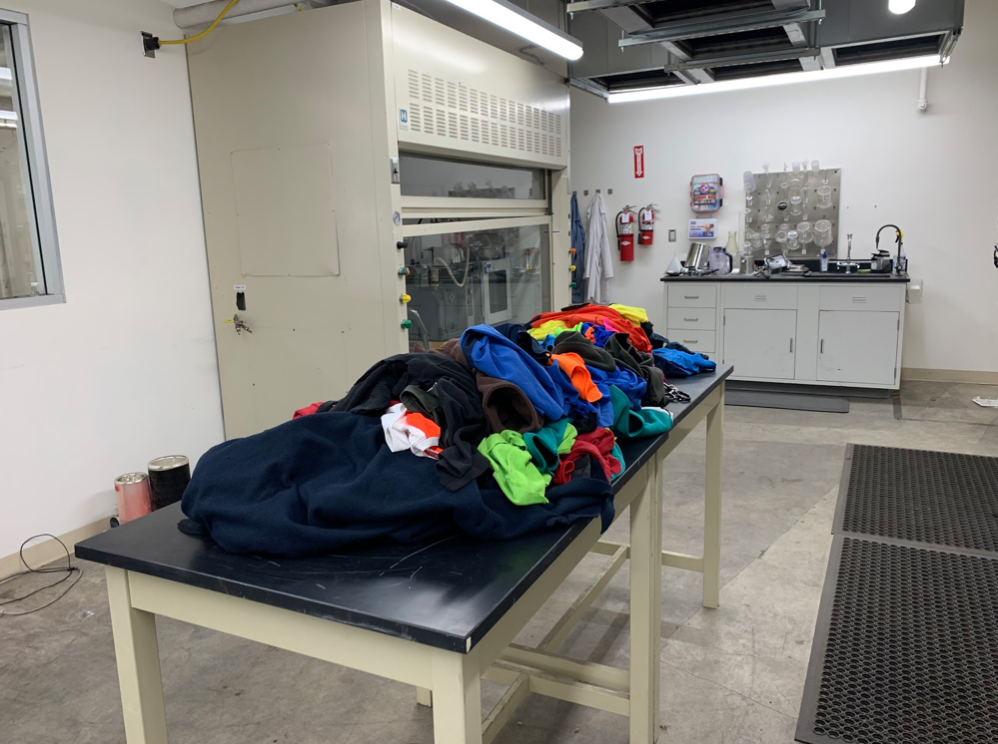
At Ambercycle, a lot was going on when the Rotterdam material arrived. The process of scaling from a laboratory to a pilot plant is non-linear, and Ambercycle wanted to move quickly. From January 2019 – April 2019 a pilot plant was built, but for a variety of reasons, this one didn’t achieve what it needed to. In May 2019, Ambercycle started building a second pilot plant. This one wasn’t perfect since it didn’t use the most sophisticated engineering, but more importantly, it worked. There are drawbacks to this, but it meant that Ambercycle could have minimum success quicker. Tests were run with a representative sample, and then produced polyester from the EigenDraads material.
The Ambercycle team had lots of discussions about the pathway of development. Start with a clean stream of garments and ratchet up feedstock complexity over time? Or start with real world feedstock. This is not an easy question to answer. But EigenDraads was the forcing function, and Ambercycle committed to working with EigenDraads first Time constraints meant Ambercycle had to just throw stuff in.
A lot of material got lost during the startup phase of the plant, developing the learning curve for the real complex feedstock. Eventually Ambercycle ended up with around 10 kilograms of polyester resin to produce a filament. To meet minimums the recycled polyester was blended with virgin polyester and went into the spinning frame. The paranoia of yarn breaks was very real. But together with good partners in North Carolina, some yarn was produced. Melt spinning and subsequent texturing were executed, with good resultant mechanical properties.
The yarn was shipped back to Los Angeles, and with the use of local partners knitted into a sports jersey on a, 18 gauge size flatbed knitting machine, amenable for our final yarn count. Through being made on a flatbed knitting machine, it was seamlessly knitted with no cut/sew wastage and it was knit as a whole garment at once via special programming. This sports jersey in collaboration with EigenDraads was the first garment Ambercycle has ever made.
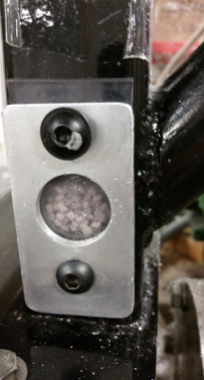
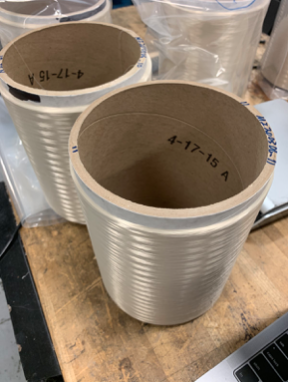
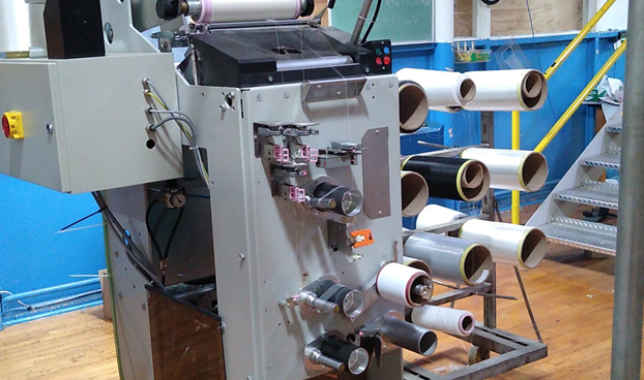
3. Lessons learned and way forward
Whilst the scale of the pilot was small, its impact was vast. In 2020, the EigenDraads team was able to show the city’s councilor that Rotterdam can play an active role in creating a recycling hub to solve the waste problem using technologies like Ambercycle’s. Whilst the city did not have ambitions on textiles in the past, she now intends to publish its own vision on circular textiles in 2021. Besides, the grant awarded to the pilot allowed Ambercycle to forcibly go through their full process at small scale – from feedstock definition to garment creation – before rolling it out commercially.
Finally, the pilot illustrated that there is still a huge gap between the fashion industry’s focus on and investment in recycling solutions, and the acute textile waste problems governments are facing. Recycling technologies like Ambercycle’s will not scale without demand for recycled content from the fashion industry. However, the immediate need for such technologies will never be known if governments do not start to investigate their use to reduce the growing mountain of valueless textile waste they are facing. This pilot should be the start of a new, public-private approach to close the loop on textiles and spinning it around.
4. Ambercycle and EigenDraads background information
Total circularity is a shared vision from EigenDraads and Ambercycle, and material re-utilization is an obvious component of a better future.
Ambercycle’s mission is to end waste. Founded in 2015, the roots are in the belief in the unbounded possibilities of science. Ambercycle is developing a chemical process to regenerate polyester from post consumer textile materials. Total circularity and infinite regeneration cycles are inevitable and Ambercycle is looking forward to helping enable a part in this transformation.
EigenDraads was established in 2018 to raise awareness on the urgency of a solution for non-reusable used textiles and to start acting and trying out potential solutions, in Rotterdam and beyond. The social enterprise is a collaboration between Hilde van Duijn and Remi Veldhoven, both circular textiles experts, with financial support from the City of Rotterdam. EigenDraads believes The Rotterdam region holds a unique position as major international transit port for used textiles and could be the ideal location to create a last resort for used, non-rewearable textiles.